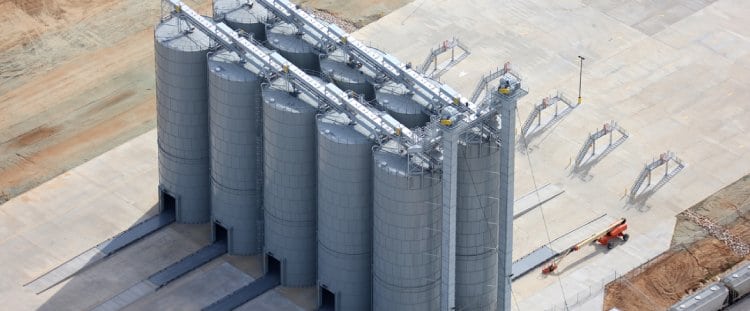
Published in the November 2016 issue of Powder & Bulk Engineering
When selecting a new bulk solids silo, determining your application’s requirements in advance can help the supplier provide an efficient, cost-effective design. This article will help you identify the storage needs to include in a request for proposal to a silo supplier.
Just because your company handles bulk solid material doesn’t mean you have to be an expert in bulk solids storage equipment. While being aware of preferred solutions on the market is helpful, you don’t have to wade through endless websites, sales brochures, and technical literature to determine the best storage solution for your application. To reduce headaches and save time and money, create a list of your application’s specific requirements before you engage a supplier. Having a clear idea of what you want to accomplish will help you ask the right questions and manage your spending judiciously.
Whether you handle food, frac sand, minerals and aggregates, chemicals, plastics, or petrochemicals, an off-the-shelf silo is unlikely to be your ideal storage solution. In addition to a wide variety of silo support options, including standard or short skirted, leg, or lug supports, your silo will likely require additional components such as dust collector flanges, manways, nozzles, flow control or internal blending devices, stairways, peripheral conveyor supports, or interior maintenance platforms. With so many potential add-ons, you should look for a supplier that can provide a variety of adaptable systems that integrate seamlessly with these components.
Your silo should be designed based on your specific application requirements, including the site location; seismic, wind, and snow loads; the material being stored; the material feed and discharge methods; how the material is being used; other equipment in use; time constraints; and your budget. When preparing your list of requirements, be sure to consider the following:
Material being stored
Let’s start with the type and amount of material to be stored because that will dictate the silo type and the necessary features. Your supplier will need to know the material’s characteristics, including particle size (such as fine powder or granular); hygroscopicity; abrasiveness; and compacted bulk density in lbs/ft3.
Consider the volume of material your application handles and make sure the silo can be built to the exact dimensions you need. Dry bulk storage silos are typically made of shop-welded steel, field-bolted steel, or concrete. (Field-welded steel silos are also available but are most commonly used for liquid applications.)
A Shop-welded steel silo is suitable for plastic resins, food products, dry chemicals, minerals, wood waste, and other miscellaneous dry products. The silo is delivered to the site in one piece, which is ideal for handling but limits the silo’s length and diameter. Maximum capacity is typically about 10,000 cubic feet, but additional storage capacity can be added by splicing the skirt to extend the silo’s overall height to greater than 140 feet.
A field-bolted steel silo is erected in place from steel panels, so it can be larger than a shop-welded steel silo, with a diameter commonly ranging from 15 feet up to 50 feet with a hopper and a capacity of up to 225,000 cubic feet. Shipping cost is lower than for a shop-welded silo, and the steel panels can be powder coated at the factory rather than painted on-site, so installation can be 2 to 3 times faster than for a shop-welded silo. A field-bolted silo can be designed to store a range of particle sizes (from fine dust to large chunks) and bulk densities (exceeding 140 lbs/ft3 in some cases). Common applications include cement, frac sand, fly ash, coal, limestone, lime, aggregates, minerals, chemicals, plastics, select foods, and wood waste.
A concrete silo is typically very large and is mainly used when the cost of bolted steel is prohibitive. A concrete silo often has a flat bottom rather than a sloped hopper bottom and may use an internal reclaimer (a screw that spins as it revolves around the center of the flat silo floor) to draw poorly flowing material into the discharge. Concrete silos are often used for storing large biomass materials, such as wood chips or fuel for alternative-fuel power plants.
How you intend to feed material to the silo and discharge material from the silo will help determine the most cost-effective size. You can sometimes save money by building a taller and narrower silo, effectively reducing the stored material’s overall downward force and minimizing stress on the silo’s hopper support.
If your material is resistant to flow or frequently hangs up, causing obstructions, make sure the silo’s interior surface is smooth and corrosion resistant. Some silos feature a baked-on, dry powder coating for smooth material flow.
Also consider whether your material’s composition, consistency, or bulk density are such that your silo will require flow-aid devices such as bin activators, vibrators, aeration, or mechanical agitation to promote flow and prevent bridging or ratholing.
Discharge Height
Consider the silo’s discharge height carefully, as this is a cost driver. For example, if the silo will be used for loading trucks, you may need a loading spout (either dustless or not) and possibly a positioner. Dustless loadout requires the addition of an integral dust collector, which can add up to 3 feet to the silo’s discharge height. A positioner can add 2 to 3 more feet depending on the unit, but this addition will increase loadout speed and reduce operation costs. If the silo is for storing incoming materials, consider how much space you’ll require below the discharge to install and maintain the equipment for conveying the material from the silo to your process.
The type of flow desired will primarily dictate the silo’s hopper slope, which also influences the discharge height. Mass-flow (first-in first-out) generally requires a steeper hopper slope than funnel flow (first-in last-out). As a result, a mass-flow hopper will likely be taller than a funnel-flow hopper, which will reduce the clearance below the discharge. You should also consider the hopper’s outlet diameter, which will affect the discharge flowrate.
Site location
The size of the area where the silo will be located will help determine the silo type and construction method. Your installation approach will also vary depending on whether the silo location is a greenfield site (new construction) or a brownfield site (adding to an existing facility). A greenfield site is a blank slate; you have a clear foundation to build on and there’s no other equipment around. When installing a silo next to existing equipment on a brownfield site, you can’t afford down time and may have tight quarters with height restrictions or equipment overhead. Make sure the supplier knows about your space restrictions and is capable of installing the silo in the area available. Accommodating a crane requires a great deal of space and sometimes great expense or interruption to your process, while a jacking system or scaffold will exceed the silo’s footprint by only a few feet.
Field-bolted silos typically come with either flat or chimed panels. Flat panels overlap vertically on all four edges, while a chimed panel has horizontal flanges along the top and bottom edges so panels fit together and form a compression seal using synthetic rubber gaskets. Chimed panels are typically assembled from the ground up using a scaffold, but flat panels are commonly assembled from the top down using a jacking system. Workers bolt each successive row of panels together at ground level and then jack up the assembled portion before attaching the next row below it. Working at ground level makes attaching components to the panels much easier compared to lifting them into place at elevation, but jack rental and other required equipment costs may outweigh the cost of additional time required to erect scaffolding. With either method, be sure to ask your potential supplier about safety systems provided and the supplier’s EMR (emergency modification rating, used by the insurance industry to measure a company’s past injury claims and potential risk). Also, confirm that the supplier’s installation methods have been approved by a third-party, professional engineer with experience in safety procedures.
If you already have a conveyor on the silo pad, building a scaffold around and above the conveyor is more effective than using a jacking system. However, if you have an existing overhead conveyor or other obstruction preventing you from bringing in a crane to lift the silo roof into place, using a jacking system to assemble a flat-panel silo at grade is likely the better solution.
Construction Time
Labor will be a significant chunk of the project cost. One of the main advantages of a flat-panel, field-bolted silo is the speed of construction using the jack installation method. This is particularly beneficial for installations that include multiple or very large silos. For example, if you’re building four silos and you’re saving a week per silo using jack installation versus scaffold installation, you’ll complete the installation a month sooner and significantly reduce labor costs. A large silo can be jack built in 20 to 25 days versus 45 to 60 using a scaffold process.
Maintenance Requirements
You should also consider what you’ll need to do to maintain high performance at minimal cost throughout the life of the silo. Make sure your silo has easy access to internal components for routine maintenance, repair, or replacement. A bolted silo uses either gaskets, sealants, or a combination of the two to seal the joints between panels, and resealing joints is another maintenance expense. When comparing silos, you should understand the properties of the gaskets or sealants used and consider the quality and testing of those materials. And since a large bolted silo may have tens of thousands of bolts, you should also ensure that the bolts used on the silo you select have the necessary strength and corrosion resistance for your application.
Finally, don’t forget to consider the silo’s appearance, especially for silos that are visible to the public. Painted silos need repainting, at great cost, while powder coatings are permanent and resist corrosion and weathering. Not all factory-applied, heat-cured coatings are created equal, however. When selecting a supplier, ask about the coating application specifications. Adhering to the coating’s application specifications is the most important factor in determining the coating’s longevity, but any factory-applied coating will typically provide better overall longevity than a coating that’s applied in the field. Also ask if the supplier tests for coating holidays (defects such as pinholes, cracks, or insufficient bonding) and, if so, using which method, according to which standard, and how frequently. Some standards only call for random visual inspection while others are more comprehensive. A 67-volt wet sponge tester, for example, signals an alarm when the tester locates a coating holiday, but a 1,100-volt tester signals an alarm and then burns through the coating to mark the holiday’s location and ensure that the defective area is recoated.
CST Contact Information:
CST Industries, Inc.
Jay Anzelmo
Dir. of Global Business Development – Dry Bulk Storage
913-982-7965
janzelmo@cstindustries.com